如何用离散余弦特征判断齿轮的状态?有什么独特的信息信号吗?|焦点简讯
时间:2023-05-20 09:03:02 来源:小姜胡侃
文|小姜胡侃
【资料图】
编辑|小姜胡侃
引言
离散余弦矩阵作为压缩感知的稀疏矩阵,由于其具有极好的能量聚集性,因此被广泛应用于一维声音信号、二维图像信息的稀疏表达。
机械振动信号作为一种类似于声音信号的一维信号,其与声音信号有很多相似的地方,因此理论上机械振动信号也能在离散余弦域上进行稀疏表达。
利用振动信号在离散余弦域上的稀疏表示,其在离散余弦矩阵中对应的稀疏系数理论上与原始信号的固有特性有关。
因此每一段信号都能在离散余弦矩阵上得到一个不同的稀疏系数,那么这个稀疏系数就包含有实际信号的很多独有特性,这些独有特性能用来进行信号的判别。
仿真信号基于离散余弦变换的分析
对此,实验中先使用简单的模拟信号进行检验,用于验证使用离散余弦变换的信号具有类似于傅里叶变换的特性也能表达信号的一部分有用信息。
实验中定义两个频率段,f1=150Hz,f2=350Hz,定义两个幅值A0=5,A1=10。然后通过构建最简单的正弦或者余弦信号进行相关实验。散信号的采样率Fs=2000,信号长度L=1000,单值信号片段如下图所见。
齿轮箱仿真信号的离散余弦变换分析
在实际运行中,齿轮箱通常都需要承受复杂的重载作用力,这些加载在齿面上的动态作用力会使齿轮轮齿承压面出现故障。
当齿轮制造的材料均匀,运行过程中相对平稳时,齿轮多出现分布式故障,即故障大致均匀的分布在齿面上,如轮齿的齿面磨损。
磨损是一个逐渐累积的过程,当轮齿表面磨损到一定程度时,齿面或齿根的强度就不足以支撑或承受较大的载荷波动了。
一旦某个薄弱节点瞬时失效,那么就可能会导致齿轮箱乃至整个传动运行系统失效,放在大环境中就是设备损坏、工厂生产线停止运行,这会带来巨大的损失。
齿轮的磨损分为三个阶段,即初期的快速磨损,中期的缓慢磨损,再到后期的快速磨损失效。
前期情况下,由于齿面磨损相对较慢,轮齿啮合条件相对较好,外部载荷在齿面上基本均匀分布,这时的振动信号也是相对平稳的,没有较大的冲击出现。
但当齿轮一旦出现较大的故障缺陷时,这时由于力的不均匀分布,会出现轮齿局部受力较大,出现载荷波动,载荷的波动放在能量角度就会出现能量不均匀的情况。
这时就出现了局部冲击,在振动信号的频谱图上我们就能发现局部频率处较大的调频和调幅现象,这就表明在当前频率段附近存在能量集中的现象,可能存在故障。
对此,我们先使用模拟信号进行测试与检验,实验使用到的模拟信号参考《行星齿轮箱振动故障诊断方法》中关于振动模型的定义。
为了不失一般性,在只考虑齿轮基频的情况下,即齿轮啮合频率和分布式故障的特征频率,定义了振动模型。它的信号离散余弦域图和调幅余弦变换包括图如下。
对比以上两图,在采样信息为Fs=2000,信号长度L=1000的情况下,从后图中可以明显发现调幅处理后对应频率处的幅值变换。
可见,经过离散余弦变换以后,发生调幅现象的齿轮箱信号的幅值相比正常情况来看有明显的幅值升高现象,这些升高的数值就表明当前齿轮箱中已经存在啮合故障。
本次实验中只是调整了一下模拟信号中相应频率处的幅值,经过调幅处理的信号在离散余弦频谱图中对应频率处的幅值的确发生了变化,只不过由于模拟信号中不再像前边模拟信号那样简单,因此无法找到幅值增长的线性关系了。
但整体分析可见,经过调幅处理的模拟信号在离散余弦频谱图上幅值却有增大。
上述齿轮箱模拟实验中信号依旧较为单一,仅有调频与调幅两部分,没有噪声的干扰,而实际采集的齿轮箱信号则成分更加复杂,不仅有不同零件啮合信息的影响,如复杂机构中执行机构、轴承等。
同时噪声的干扰也很大,有时候采集到的信号中由于噪声干扰太大,有用信息完全被噪声淹没,因此对于实际信号的分析才更有研究意义。
齿轮箱实测信号基于离散余弦基的特征提取分类
实验中采集齿轮箱太阳轮的5种信号,分别为太阳轮正常、太阳轮断齿故障、太阳轮缺齿故障、太阳轮齿面磨损故障、太阳轮齿根裂纹故障。分别对行星齿轮箱太阳轮5类信号进行采样分析,观察这5类信号基于离余弦变换以后在对应频率处的幅值变化情况。
上表中罗列出该频率段附近的幅值变换;实验中为了提高信号稀疏度,选取采样信息为Fs=20000,L=5000,前边实验中已经描述过,当Fs=4×L时幅值变换发生在原频率一半位置处。
通过分析表中的数据可以发现,行星齿轮箱太阳轮故障信号与太阳轮正常信号对比,其在相应频率处的幅值会有升高的现象。
由于实测信号成分复杂,因此在对应频率处的幅值信息不好捕捉,又因为故障不仅会引起正常信号成分的调幅变换同时还会影响正常信号成分的调频现象,因此在对应频率处信息捕捉时找理论频率附近的3个幅值作为采样信息。
上表主轴转频处的幅值信息柱状图,从图中能够直观的发现,当行星齿轮箱太阳轮存在故障时,在主轴转频处的幅值信息发生了明显的变换。
当有故障时,故障轮齿的幅值明显高于太阳轮正常情况下的幅值信息。
用同样的方法画出啮合频率处的幅值信息柱状图,参考下图。
与上图中的现象类似,当行星齿轮箱太阳轮存在故障时啮合频率处的幅值信息明显比正常情况下的大,但也有部分信息稍大或者相近的情况,这可能有实验时没有加载有关。
因此使用离散余弦变换时我们虽能找到信号对应频率处存在调幅现象,表明在当前频率处可能存在故障,但对于一些调频现象引起的幅值变换我们还不能准确的加以判定,这就为基于离散余弦变换的频谱分析带来了一定的影响。
事实上,我们还是能够发现,对于行星齿轮箱太阳轮在缺齿、断齿等局部故障情况下,由于局部能量的集中,其对应频率处的幅值变化还是很大的。
而齿面磨损这类型分布式故障情况下,由于载荷或能量集中不像局部故障那么明显,所以在对应频率处的幅值变化相比太阳轮正常情况下而言会小一些,这就造成故障不容易被判别出来。
对于齿轮分布式故障来说,一个可能的影响是实验中阻尼器上加载的外载荷的大小;当外载荷太小时,的确会出现调幅现象不明显的情况。
下图为行星齿轮箱太阳轮正常情况下,采集到的信号经过离散余弦变换以后的频谱图,图中大致标出齿轮啮合频率和一些传动零件啮合频率处的幅值。
从图中可见,实测信号的成分相当复杂,想要找到信号对应啮合信息处的幅值信息点并不容易。而且实测故障信号不仅会对原信号产生调幅影响,同时还会产生调频影响,这种情况下基于离散余弦变换的频谱分析就会受到干扰。
实际生产中得到的信号往往是非线性且带有一定的波动性的,同时故障点的出现具有瞬态性,没有特定的规律可言,这就为基于常见的时域、频域分析带来极大的干扰,使基于这些方法的信号分析不能很好的捕捉到信号的故障特征。
应用离散余弦变换分析故障时,需要将得到的离散余弦变换频谱图局部放大,然后在对应频率附近找到相应的幅值点进行数据标记,这也会造成误差,并且会耗费大量的人工和时间。
尽管也能进行故障判别,但这种办法显然费时费力,需要利用计算机的计算能力对故障进行高效的判断。
信号基于稀疏矩阵得到相应的稀疏基是与信号一一对应的,同类信号不同片段的稀疏基在波形上、系数上类似,但并不相同,这也与实际信号的非线性、波动性有关。
但稀疏基对应于原始信号在稀疏矩阵上的稀疏表达形式,其完整的展现了信号在稀疏矩阵上的所有有用信息,因此稀疏基相当于变维度的信号表达形式。
基于上述特征,我们就可以基于信号在离散余弦矩阵上的稀疏基进行信号分析、判别,观察是否存在较好的对比参数。
下面5个表分别为行星齿轮箱在太阳轮断齿、缺齿、正常、齿根裂纹、齿面磨损5种情况下选取每类信号的4个片段进行离散余弦变换后基于其对应的离散余弦基进行的特征提取。
从中我们能够发现,基于峭度特征的数值,在行星齿轮箱太阳轮正常情况下的数值较其它4类故障的对应数值明显偏大,因此我们选择基于信号离散余弦基的峭度特征用于判定行星齿轮箱太阳轮是否正常的标准。
由于上述5个表中选择的信号片段较少,每类信号只选择了4个片段进行的实验,为了提高准确率,再选择不同类型信号上的10段不连续片段进一步验证上述理论。
下表为选择行星齿轮箱5种不同信号的10个不同片段进行离散余弦变换后对其对应的离散余弦基进行的峭度特征提取。
从数据上看,在太阳轮正常情况下其峭度数值明显要比其他四类信号的相应数值要大,那么就能据此判断当前信号是否存在故障,为了更直观的查看,将下表中的数据转换为折线图的形式。
由下图和上表中对比数据的直观表现形式,从折线图中可以发现,行星齿轮箱在太阳轮正常情况下其离散余弦基的峭度特征与4类故障情况下的曲线有较为明显的区别。
折线图中对判别造成干扰的是行星齿轮箱齿根裂纹故障下的对比参数,这与实验前输出轴未加载外部载荷或者加载外部载荷较小有关。
因为在未加载外部载荷或者外部载荷较小的情况下,齿轮承压面上的力仍旧是均匀分布的,这时齿根处的应力应变仍旧在材料承受极限内,因此会表现出与正常情况类似的现象。
笔者观点
基于上述对比实验分析,我们能够清晰的发现,行星齿轮箱信号的离散余弦基峭度提取能够进行故障判别,相比于同样基于离散余弦变换的频谱分析。
这种方法计算速度更快更便捷,同时也不会受实际信号非线性、动态波动造成的频谱分析不便的影响。
因此在信号进行压缩感知故障分类判别时,能基于离散余弦矩阵对信号进行快速故障预判。
参考文献
[1]李飞.基于压缩感知与扩展双谱的齿轮振动信号特征提取方法研究[D].西南交通大学,2018。
[2]刘畅.基于压缩感知的滚动轴承特征提取与特征约简方法研究[D].昆明理工大学,2017。
[3]任伟军.基于参数优化的MOMEDA与压缩感知的高速列车滚动轴承故障诊断研究[D].北京交通大学,2021。
[4]闫常弘.基于压缩采集的轴承智能故障诊断方法研究[D].燕山大学,2018。
[5]王超.基于压缩测量的机械装备智能故障诊断技术研究[D].兰州理工大学,2020。
标签:
最新文章推荐
- 如何用离散余弦特征判断齿轮的状态?有什么独特的信息信号吗?|焦点简讯
- 截至今年4月底 河北诚信计量自我承诺单位达10520家
- Steam Deck升级FHD+屏售99美
- 过户费怎么算二手房_60万的商住楼过户费包括哪些
- 单面镜和双面镜的测试方法_单面镜 天天讯息
- 股票行情快报:普蕊斯(301257)5月19日主力资金净卖出172.31万元 今日快讯
- 武汉博物馆(关于武汉博物馆介绍) 速递
- 中国-中亚峰会|爱种草莓的王倩:将先进种植技术引入乌兹别克斯坦
- 熟食小龙虾外卖缺斤少两?江苏省消保委建议加大惩戒力度
- 全球热资讯!“梅沙—乐业、凌云”东西部旅游协作和旅游共建消费帮扶活动正式启动
- 徐汇区举行“15分钟社区生活圈”行动工作推进会
- 焦点日报:美少女梦工厂4魔化程度_急求美少女梦工厂4魔嫁问题
- 观热点:新生儿医疗保险如何办理流程?新生儿医疗保险什么时候办最好?
- 世界即时:WE分享选手返图:Cube快速融入与香掌门密切互动
- 【全球聚看点】三线崩盘,AC米兰乱了,红鸟表态,开除马尔蒂尼,清洗4人,保帅
- 生态环境部启动2023—2024年黄河流域“清废行动”
- 文明村镇|“一荒变四园” 乡村展新颜
- 每日报道:全国农产品批发市场猪肉平均价格为19.35元/公斤 比昨天下降0.4%
- 宁波唐狮网络科技有限公司
- 珠海港董秘回复:截止至2023年05月10日,公司股东总户数80,335户(不含信用证券账户) 世界新要闻
X 关闭
资讯中心
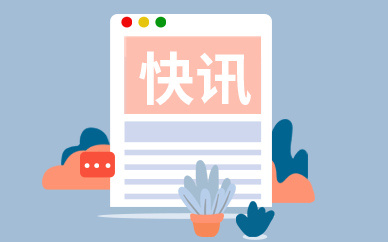
2022-08-06
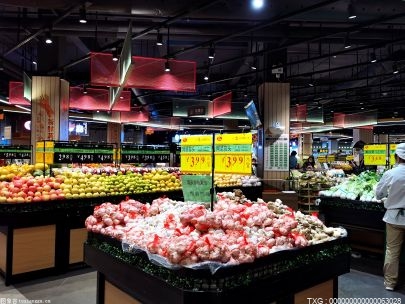
2022-07-08
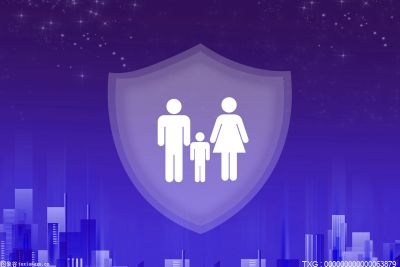
2022-05-20
2021-10-18
X 关闭